Description
Do you need a rubber mixer mill to mix your rubber products and knead just the way you want them?
Look no further than the Rubber Mixer Mill with Water Cooling System – a reliable machine that can easily handle all sorts of rubber material. Featuring dual output reducers, rolling bearing mixing, and fast processing speeds, this machine is ideal for those who need to get their products mixed quickly and without any complications.
This laboratory mixing mill machine is designed to handle rigid materials while incorporating water cooling technology to ensure that the machine rolls are always at a balanced temperature. Its safety features make it ideal for those who want to operate their machinery efficiently. So, if you’re in the market for a high-quality machine that is sure to add a touch of sophistication to your workplace, Rubber Mixer Mill with Water Cooling System is a perfect choice!
Made from high-quality materials and fitted with state-of-the-art technology, this two roller mixing mill machine is bound to make your job easier. Plus, its emergency stop function makes it easy to avoid accidents.
The rubber open mixing mill machine is a plastic material mixing equipment with an adjustable gap between two parallel rollers. Its main function is to mix and plasticize uniformly mixed raw materials. Geared motors independently drive the roll; when processing, these two rolls would rotate at different speeds in relative directions.
After kneading and mixing for some time, the internal macromolecular chain would be broken accordingly so that the various components inside the rubber compound are evenly mixed and dispersed. Its physical properties and chemical effects would change and contrast.
These lab roll mill machines are widely used in the rubber and plastics industries, such as polyolefin, PVC, film, coil, profile production, polymer blending, pigments, masterbatch, stabilizers, stabilizers, and so on.
The rubber mixing mill serve lot of essential functions in various industries 1. Rubber Processing : Perfect for mixing ,kneading and blending rubber compounds ,which ensure uniformity and consistency in your final products 2. Manufacturing : The mixing mill are ideal for the production of rubber sheets ,belts ,tires and other rubber-based products with precise specifications and quality control. 3. Research and Development : Facilitates experimentation and testing of new rubber formulations,enabling innovation and improvement in product performance. 4. Quality Assurance : Guarantees the integrity of rubber compounds by thoroughly mixing ingredients ,eliminating air bubbles and dispersing additives evenly. 5. Customization : Offers fleibility in adjusting mixing parameters to meet the unique requirements of different rubber formulations and applications .
Steps in the Rubber Mixing Process
1. Introduction of the Polymer
The rubber mixing process begin from the introduction of the polymer, the basic structure of rubber compounding. The choice of polymer material contribute to the foundation for the material’s performance and dictates its inherent characteristics.
2. Sequenced Addition of Ingredients
While the polymer typically has the largest impact on the characteristics, additional ingredients are added would determine its features ,including curing and processing performance, consideration of production cost , hue designation, anti-degradation, and many other . This may be fillers, plasticizers, curing agents, accelerators, etc.
3. Achieving Homogeneity in the Compound
The ultimate goal is to achieve thorough homogeneity. Through well-mixed and blended of all ingredients ,it would create a uniform and consistent rubber compound. A homogeneous rubber compound ensures uniform characteristics throughout production processing, curing and the final application of finished rubber goods. This is achieved by carefully adjusting the several key mixing parameters according to the compound requirements while carefully considering chemical interactions of ingredients. Each rubber compound performs and reacts differently to the process. Therefore , to create a ideal mixture ,it requires an experienced operator execute on each compound’s detailed and exact mixing procedure .
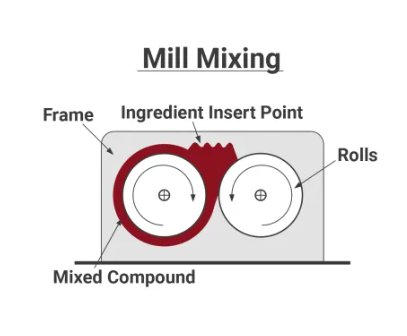
Nip Gap adjustment is Motor Driven
Operating Panel Combination of touch screen and PLC-control allows comfortable operation of the machine
The Rubber Mixing Mill Serve Many Functions in Various Industries
1. Rubber Processing : Perfect for mixing ,kneading and blending rubber compounds ,which ensure uniformity and consistency in your final products
2. Manufacturing : The mixing mill are ideal for the production of rubber sheets ,belts ,tires and other rubber-based products with precise specifications and quality control.
3. Research and Development : Facilitates experimentation and testing of new rubber formulations,enabling innovation and improvement in product performance.
4. Quality Assurance : Guarantees the integrity of rubber compounds by thoroughly mixing ingredients ,eliminating air bubbles and dispersing additives evenly.
5. Customization : Offers fleibility in adjusting mixing parameters to meet the unique requirements of different rubber formulations and applications .
Application of Two Roll Mills
*PVC powder mixing and colour sampling
*Polymer milling mixing
*Plastics formulation mixing test
*Rubber mixing test
*Material development, material testing, quality control, education
*Raw rubber ,Synthetic rubber ,Thermoplastics or EVA with chemicals
*Polymer like LDPE, HDPE, PP, PVC, PS, ABS, HIPS, Natural Rubber, EVA etc. can be tested.
Benefits of Chosing Simptek Rubber Mills
* Enhanced productivity : Increase your production efficiency with this high-capacity kneader, reducing processing time and enhancing overall output.
* Consistent Quality :Achieve unparalleled consistency in rubber compounds ,satisfying the most stringent quality standards with every batch.
* Versatility : Suitable for a wide range of rubber formulations and applications , also applied for diverse industry needs .
* Reliable Performance : Experience reliable and precise mixing ,ensuring uniform dispersion and superior product quality .
Reviews
There are no reviews yet.