Description
Lab silicone mixing mill is also know as lab two roll mill ,open double-roll refiners ,it feature with two hozizontally arrange and rotating rollers to process and mix various polymers in small batches for academic research and small-scale experimental use.
This Two Roll Rubber Open Mixing Mill is an amazing combination of innovation and technology that serves the purpose of mixing and kneading various forms of plastics and rubbers. The products industry of plastics and rubbers is raw rubber, synthetic rubber, thermoplastics, polymers, PVCs, EVA or Color masterbatch. It is highly usable in the industry that deals with plastics and rubbers.
The machine comprises rigid chrome plates that are mirror polished and anti-corrosive. The plates are highly resistant to the high temperatures, thus allowing the machine to work in a very systemized way as the material that is the result of the processing of this two-roll mixing mill is further used to feed calendars, hot presses, and various other kinds of machines that are used to manufacture and process multiple types of rubbers and rubbers and plastics.
The laboratory two roll mixing mill equipment is suitable for mixing, kneading and dispersing various chemical raw materials elastomeric and thermoplastic polymer samples. The materials to be mixed are placed in the roll nip gap. With the desired temperature, nip gap and friction, the materials are mixed in the nip after several roll turns to form a homogeneous mass.
In the rubber plastic industries ,this laboratory open mixing mill is widely used to masticate raw rubberor synthetic rubbers including NBR ,SBR,BR etc to achieve the required plasticity character. Besides ,this lab two roll mill equipment is also used to repeatedly disperse and incorporate raw rubber with various additives including accelerators ,fillers,vulcanizing agents etc ,so that obtain a uniform rubber compound for further molding and processing for laboratory use. While in the plastic industry ,this laboratory two roll mill equipment is widely used for plasticizing and mixing resins with other additives in small batches to obtain sheet material of specified thickness with even dispersion and good interpenetration between components for laboratory recipe development ,color comparison ,trial production ,molding ,aging text etc.
Such Rubber crumb/reclaim, Rubber Refiner Mill are widely used in new tyres/tubes, devalcanisation for low-tech pressed or extruded rubber products, tread rubbers, belting, battery containers, molded item, commercial flooring, traffic control products and plenty more.
We ,Simpek Machine ,as one leading manufacturer of rubber processing machine , custom design and made various size Laboratory Open Mixing Mills , depending on the kind of raw material to be blended ,the size rang from 3” to 24” for compounding, warming, sheeting of various grades.
Our Open Mixing Mills equipment can be equipped with a specially designed Stock blender to assist the operator in mixing the rubber material and chemical powder. With the blender stock,it would reduces the labor indulgence, providing safer working conditions, and lowering the material temperature and speeding the mixing rate of the compounds. The speed of the stock blender can be changed as per your specific needs .
The Basic Components of a Rubber Mixing Mill Include
A Rubber mixing mill is indispensable in various industries where precision and quality are paramount, such as in the production of automotive tires,footwear, belts, hoses, and gasketsspong and other rubber silicone industrial etc.
* Roller System: Two or more steel rollers rotate in opposite directions to mix and knead the rubber and additives.
* Heated Rollers: For curing the rubber material during the mixing process.
* Control System: For controlling the speed , temperature, and pressure of rolls during mixing process.
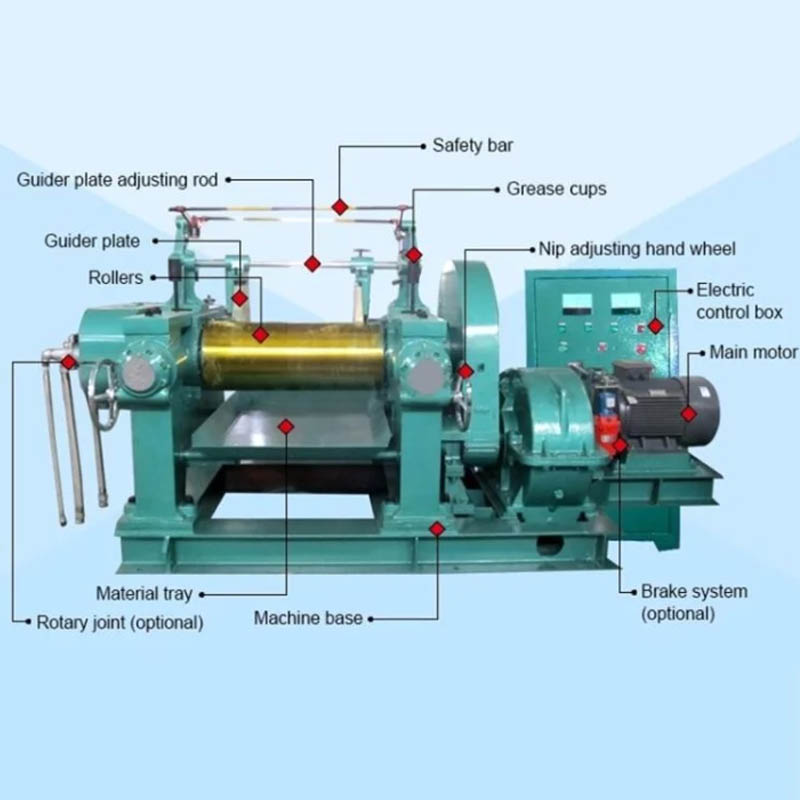
Design Features of The Laboratory Mixing Mills
* Material of Rolls – Chilled Cast Iron hollow ground finished, for even heating & cooling (Surface hardness of 480-540 BHN)
* Roller bearing – Anti-friction Spherical Roller Bearing
* Housing – made from graded Cast Iron of high quality casting free from holes & casting defects
* Column Frame – Two Nos. made of graded Cast Iron as per housing material
* Base Frame – Steel fabricatedmono-block base for perfect alignment of mill and drive.
* Standard Accessories – Gear Covers, Safety Trip rod, Return water rotary joints
* Motor- Electric any standard make
Steps in the Rubber Mixing Process
1. Introduction of the Polymer
The rubber mixing process begin from the introduction of the polymer, the basic structure of rubber compounding. The choice of polymer material contribute to the foundation for the material’s performance and dictates its inherent characteristics.
2. Sequenced Addition of Ingredients
While the polymer typically has the largest impact on the characteristics, additional ingredients are added would determine its features ,including curing and processing performance, consideration of production cost , hue designation, anti-degradation, and many other . This may be fillers, plasticizers, curing agents, accelerators, etc.
3. Achieving Homogeneity in the Compound
The ultimate goal is to achieve thorough homogeneity. Through well-mixed and blended of all ingredients ,it would create a uniform and consistent rubber compound. A homogeneous rubber compound ensures uniform characteristics throughout production processing, curing and the final application of finished rubber goods. This is achieved by carefully adjusting the several key mixing parameters according to the compound requirements while carefully considering chemical interactions of ingredients. Each rubber compound performs and reacts differently to the process. Therefore , to create a ideal mixture ,it requires an experienced operator execute on each compound’s detailed and exact mixing procedure .
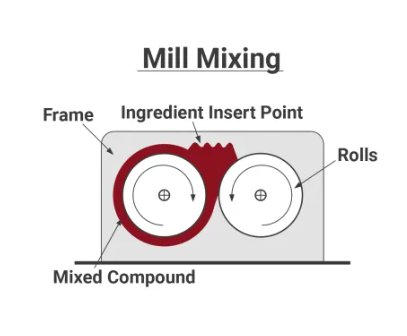
Safety Feature
*Emergency brakes with limit switch
*Emergency brakes Chest bar with reverse INCH facility provided
*Emergency brakes Provided on both sides to stop machine in ⅓rd Revolution of Front Roll
*Auto reversible control panel
*Hydraulic & Electromagnetic Thruster Brakes
Applications of Rubber Mixing Mills
* Foorwear Production : Mixing components is vital to making shoes & footwear
* Hot-melt adhesives
* Technical ceramics
* Manufacture of abrasives
* Graphite compounds
* Sealing compounds
* Hard metal compounds
* Crushing, mixing and pressing of recycled rubber.
* Recycling and processing of waste rubber materials
*Tire Manufacturing: In tire production, the laboratory dispersion kneaders are essential for mixing natural or synthetic rubber with various additives, such as fillers, plasticizers, and vulcanizing agents. Our equipment precisely controls temperature and pressure during kneading, enhancing tire grip and wear resistance.
*Rubber Product Compounding: Dispersion kneaders are widely used to produce rubber compounds like sealants, silicone rubber ,gaskets, hoses, and conveyor belts. Efficient mixing and material distribution enhance the physical properties of rubber, such as strength, elasticity, and chemical resistance, making our equipment suitable for the automotive, aerospace, and construction industries.
*Polymer and Chemical Processing: In the polymer and chemical industries, this laboratory dispersion kneader produce rubber and plastic products such as films, sheets, adhesives, and Pharmaceutical industry.
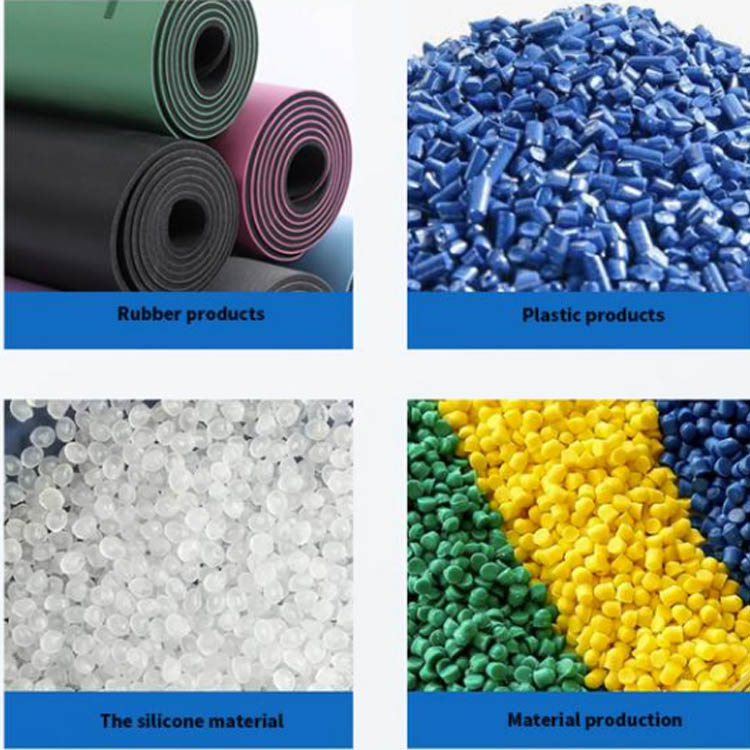
Advantages of Simptek Premium Two Roll Mixing Mills
*The rollers are made of vanadium and titanium metal alloy cold hard cast iron, with hard and wear-resistant surface
*Space-saving and ground-level installation
*Twin-drive with separately adjustable speed / infinitely variable friction
*Modern PLC based on Siemens S7 components with touch panel
*Energy-efficient – potential energy savings of up to 30%
*Low noise level
*Low maintenance and repair costs
*High quality
Operational Considerations
Manual Operation: The operation of this two-roll mills often requires manual operation, such as cutting, folding, and rolling the material on the front roll. This ensures the homogeneity of the mixture but it would be strongly to operate by skilled operators.
Safety Systems: The two-roll mixing mills are usually equipped with safety systems to ensure the safety of operator, providing maximum comfort and reducing the risk of accidents during operation.
Reviews
There are no reviews yet.