Description
Simptek offer a wide range of most advance and high quality Open Mixing Mills which are also known as two roll mill at competitive cost to the clients.
Our in-house capabilities and expertise rival any of our competitors. Regardless of the size or brand of mixer, our rebuilding services are of the highest quality and offer the best return on your dollar.
Two roll rubber mixer is used for mixing and kneading raw rubber, synthetic rubber, thermoplastics ,silicone ,polymer or E.V.A.with chemicals into even materials, so that these manufacturing factories get best mixing dispersion of ingredients and raw rubber.
This 24inch large capacity rubber mixing mill machine is equipped with stock blender, it would save labor and increase productivity on process.
The main part of two roller rubber mixing mill machine is the two hollow rollers ,well known as drilling hole rollers, which rotate in different directions & speed.
The roller are made of very hard chilled alloy cast iron, whose surface is high glossy and hard. These two roller’s diameter usually is the same, the raw rubber material will be involved in the gap between these two rollers with the rotation of roller, subjected to strong shear to achieve the purpose of plasticizing or mixing.
The two roller plastic polymer mixing mill adopts dual high grade output reducer, which allow the noise is very low when it is running. And the front and rear roller can be driven separately by two motor with rolling bearing structure, the roller can be used hollow center groove roller or drilling hole smooth roller against difference using scope as mixing.
This two roller open mixing mill with stock blender is mainly used for rubber products factory, like natural rubber refining ,raw rubber and compound ingredient mixing,warming refining and sheeting of glue stock. This two roller mixing mill machine can reassure well lubricating and easy operation by adopting oil cup lubrication.
The laboratory mixing mills equipment ensures that natural or synthetic rubber is evenly mixed or blended with other compounds raw mateiral ,which may be of rubber, plastic, silicone , EVA , polymer or tile compound etc.
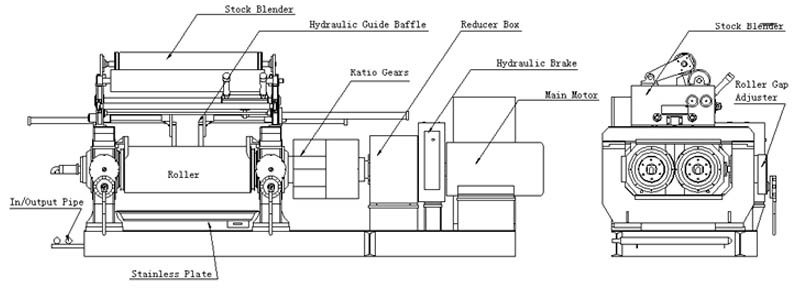
Steps in the Rubber Mixing Process
1. Introduction of the Polymer
The rubber mixing process begin from the introduction of the polymer, the basic structure of rubber compounding. The choice of polymer material contribute to the foundation for the material’s performance and dictates its inherent characteristics.
2. Sequenced Addition of Ingredients
While the polymer typically has the largest impact on the characteristics, additional ingredients are added would determine its features ,including curing and processing performance, consideration of production cost , hue designation, anti-degradation, and many other . This may be fillers, plasticizers, curing agents, accelerators, etc.
3. Achieving Homogeneity in the Compound
The ultimate goal is to achieve thorough homogeneity. Through well-mixed and blended of all ingredients ,it would create a uniform and consistent rubber compound. A homogeneous rubber compound ensures uniform characteristics throughout production processing, curing and the final application of finished rubber goods. This is achieved by carefully adjusting the several key mixing parameters according to the compound requirements while carefully considering chemical interactions of ingredients. Each rubber compound performs and reacts differently to the process. Therefore , to create a ideal mixture ,it requires an experienced operator execute on each compound’s detailed and exact mixing procedure .
Technique
Adjustable gap | 0~10mm |
Roller speed ratio | 01:01.2 |
Roll gap | 4mm |
Reducer | 5.5KW |
Motor Type | Y132M2—6 |
Power | 5.5kW |
Speed | 960r/min |
Mixing capacity | 0.2-5kgs |
Roller temperature | normal temperature~260°C |
Heating time | normal temperature ~150°C about 15min |
Heating mode | electric heating |
Temperature accuracy | ±3.5°C |
The drum in vitro thermometry | the installation of temperature the meter then extend the line |
to the thermostat temperature measurement digital display | |
Temperature control | PID controller make in Taiwan |
Roller revolving speed | fixed speed(24 revolving/min) |
Roller hardness | HRC 50~60(Made in Taiwan) |
Roller processing | Polished |
Baffle material | PTFE material, made of sharp type |
Safety device | Multiple touch, touch emergency stop, safe operation |
Power | AC380V,20A, as per your local voltage |
Motor power | 20KW |
Outside dimension | 1100×700×1200mm |
Weight | about 580kg |
Advantages of Two-Roll Mills
* Temperature Control: The temperature would increase for most machine when they are runing . Thanks to ts latest technology adopted on this laboratory two-roll mills ,it would maintain low temperatures during the mixing process due to high surface contact with cooled rollers, which is very crucial for materials that are sensitive to heat.
* Efficiency and Precision: The two-roll mills offer precision, consistency, and efficiency, making them indispensable in various industries where high-quality products are required. This two roll mills would help you to achieve specific material properties and ensure uniform mixing.
* Versatility: The mills are versatile and can be used in a wide range of applications, from small-scale laboratory work to large-scale manufacturing. This equipment are applicable many material ,including rubber ,plastic,polymer ,silicone ,chemical ,color masterbatch etc.
Application of Two Roll Mills
*PVC powder mixing and colour sampling
*Polymer milling mixing
*Plastics formulation mixing test
*Rubber mixing test
*Material development, material testing, quality control, education
*Raw rubber ,Synthetic rubber ,Thermoplastics or EVA with chemicals
*Polymer like LDPE, HDPE, PP, PVC, PS, ABS, HIPS, Natural Rubber, EVA etc. can be tested.
The Rubber Mixing Mill Serves Many Function Across Various Industries
1. Rubber Processing : Perfect for mixing ,keading ,and blending rubber compounds ,which ensure uniformity and consistency in the final product.
2. Manufacturing : Ideal for the production of rubber sheets ,belts ,tires ,and other rubber-based product with precise specifications and quality control.
3. Research and Development : Facilities experimentation and testing of new rubber formulations ,which enable innovation and improvement in product performance .
4. Quality Assurance : We guarantee the integrity of rubber compounds by thoroughly mixing ingredients ,eliminating air bubbles , and dispersing additives evenly .
5. Customization : We offer flexibility in adjusting mixing parameters to satisfy your special requirements for different rubber , plastic ,silicone formulations and applications .
Our Extensive Services Include
* Complete Inspection, Estimates and Documentation Hydrostatic and Ultrasonic Testing
* Rotor and Chamber Reconditioning, Hard Facing, and Chroming
* New improved Chamber Design for some sizes and brands
Ingredient Controls Integration
* Design Upgrades (e. g. Dust Stops, Chamber Hood, Drives, PLC control )
* Auxiliary Equipment (e.g. Weigh & Skip Hoist Conveyors, Oil Injection Units, Rebuilt Mills)
* Manually or Motorized Operated Nip adjustments with numerical controls available
* Availability of used rebuilt mixers in variety of sizes and brands
Benefits of Chosing Simptek Rubber Mills
* Enhanced productivity : Increase your production efficiency with this high-capacity kneader, reducing processing time and enhancing overall output.
* Consistent Quality :Achieve unparalleled consistency in rubber compounds ,satisfying the most stringent quality standards with every batch.
* Versatility : Suitable for a wide range of rubber formulations and applications , also applied for diverse industry needs .
* Reliable Performance : Experience reliable and precise mixing ,ensuring uniform dispersion and superior product quality .
Operation of Rubber Mixing Mill with Stock Blender
The STOCK BLENDER is installed on two roll open mill machine ,it is unique combination of stock blender rollers with transverse movement of the carriage for improved quality of compounding of material.
The compound material is taken from the front roller of the open mixing mills, which can be setted either on one side as per customers’ requirement , and then put through the transverse carriage on to the blender roll nip. The strip width of roller can vary from 180 to 240 mm. When you want to cut the strip the operator ,you need to use the cutter installed on the two rolls plastic silicone mixing mill.
The operator takes the strip and put it through the transverse to the roll of the blender. The balance compound material transverse to the roll of the blender. And the balance compound would be continuously pulled by the first strip and the whole material begin passing through the nip.
Until now, the transverse can be started so that the full width of the compound is accepted by the blender continuously from the front roll of the mixing mill machine and then fed back in the nip of open mixing mill machine.
The strip is then put in the opposite diagonal position , therefore efficiently dispersing for any additives that might need to be mixed or added on the rubber open mixing mill machine . Once the blending process is complete , the transverse carriage can be stopped and the material can be cut so as that no more material goes into the blender from the front roll.
Reviews
There are no reviews yet.