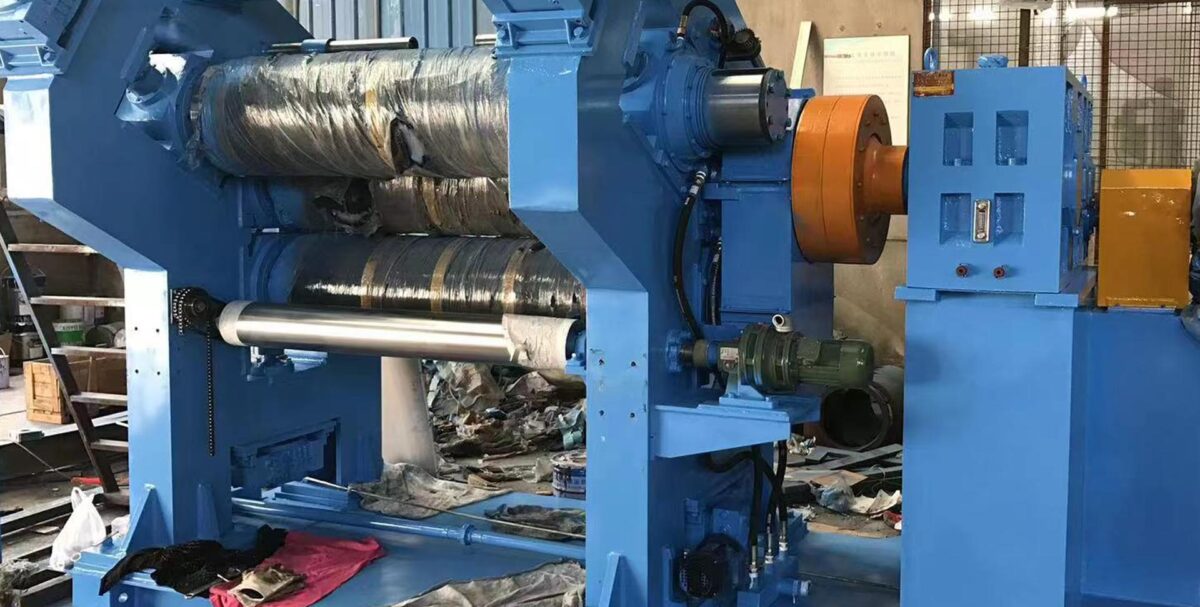
Brochure
Get a Quote
Fill all information details to consult with us to get sevices from us
Calendering Machine
Calendering is one mechanical process that plays a important role in all our darily lives. It involves passing paper, textiles, fabrics,nonwoen,tire cord, cloth, EVA ,silicone rubber or other plastics such as PVC, vinyl etc through two or more heated hard steel rolls. This continuous process compresses and smooths the material, and finally create uniform standalone sheets with specific width and thickness.
The use of calenders is mainly used to produce flat, compact and polished fabric,which is still very popular in nowsdays daily life. The rolls of calendering machine are made from chilled alloy cast iron whose surface hardness reach up to 500 Bhn. The rolls are hollow in the center for cooling/heating . By way of rotating, the rollers apply pressure,which stretch and flatten the rubber into a uniform sheet.
Actually , from disposable diapers to dryer sheets, to disinfectant wipes, to rubber tires, to PVC films used on laminate floors, to healthcare protective equipment, and many more – calendering is vital to the production of thousands of products used every day.
However, most of us may don’t know what calendering is.
Rubber Calender is a machine used to process rubber material to a specific thickness and surface smoothness. It is mainly used to produce superior rubber which is used in products like gaskets,seals and O-ring instead of normal rubber . Calendering is a method of producing plastic film and sheet by squeezing the plastic through the gap (or ‘nip’) between two counter-rotating cylinders.
The calendering machine can be adjusted for pressure and speed to achieve different thicknesses, surface finishes, and textures, resulting in products that can be shiny, matte, smooth, adherent, or embossed. This continuous calendering process compresses and smooths the material, creating uniform standalone sheets with width and thickness. These process material can be used directly or further processed to create final products.
As the rubber material is forced between the rollers ,which gets heated and causes the rubber material to deform and makes the rubber extra pliable . It is an associate degree ironing method that smooths out rubber as it is forced between the rollers stressed. The material’s character and change may be caused by controlled thickness, surface finish etc. In addition , through the procession of sheeting, the calendering machine can also press out the air in the material ,so that produce the products without air bubble after cure.
Here are the main parts of calendering machine
* Normal parts of a calendering machine for textile are as follows
* Winder
* Metal detector
* Seam detector
* Rollers (cotton, reclon and steel)
* Anti static rod
* Oscillating roll
* Batcher sensor
* Cooling drum
There are different types of calender machine, as listed in the below:
* Friction calendaring machine
* Schreiner calender
* Nipco-Flex calender
*Felt calender
* Embossing calender
* Swizzing or swissing finish
* Chasing finish
* Moiré calender
* Ciré calender
We can customize and supply all kinds of high quality calendering machine , in varied ranges and specifications. These calendering machines are manufactured by adopting the latest and most advanced technology . Moreover, we make sure to deliver the ordered consignments at the clients’ premises within the stipulated time frame.
According to Simptek technology ,our calendering machine can be divided into paste calender, friction calender, tablet pressing machine, pressure type rolling machine, laminating calender and experimental rolling machine and other. the number of roller can be divided into two roller calender, three roller rolling mill, four roll calender, roll calender and multi roller rolling machine and other.
The roller arrangement can be divided into type I calender, L type calender, Z type calender, s type calender and other form of rolling machine.
In the plastics industry calendering is a method for producing vinyl film or sheeting. Resin,plastic,PVC,EVA or other ingredients are blended and formed into a hot plastic mass, then passed through the hot rollers of the calender. The plastic are formed as a flat film or sheet whose thickness and unformity is determined by the gap of rollers of the calender.
Simptek custom calender machines for various industries manufacturers all over the world . The calenders conprise of 2 ,3 or more steel rolls that under high pressure to smooth, compress, and in some cases partially bond a nonwoven, plastic, textile , PVC, paper, rubber or another substrate. Basically , the more quantity of rollers the calendar has, the more times of the sheets are pressed and it would make higher quality and more even thickness of sheets. The rollers may be mirror-smooth, embossed with a pattern, or porous, and are usually heated with hot oil or electric elements.
How does a Calendering Process Work?
Step 1. Material Preparation
For these material which need to be calendered ,they need pre-treatment processes such as drying, softening, or impregnation . Before being fed into the calendering machine, the material may need pre-treatment processes such as drying, softening, or impregnation to prepare it for calendering.
Step 2. Roller Arrangement
The calendering machine consists of a series of cylindrical rollers, typically made of steel material,whose hardness can reach up to 65hrc, arranged vertically or horizontally. The number of rollers can vary depending on the desired effect and the material being processed.
Step 3. Passing Through Calender Rolls
The material is then passed through these calender rollers,which can be heated or cooled, that depends on the material and the desired outcome.
Step 4. Controlling the Rolls
The speed, temperature, and gap between the rolls can be adjusted to control the degree of calendering. The calendering roller can be adjusted for pressure and speed ,so that achieve different thicknesses, surface finishes, and textures. It would resulte in products that can be shiny, matte, smooth, adherent, or embossed .
What Benefit That Calendering Can Bring?
1. Tensile Strength of Calendered Sheet
Calendering process increases the strength by coating the rubber on each side of substrate
2. Smooth End Calendering
* The calendering machine disembarrassed imperfections on the surface of the rubber .
* Calender with patterns helps in the manufacturing of profiled or marbled sheets.
3. Thickness Rolling of Rubber Calendering Sheet
* It controls thickness by adjusting the gaps between roller housing ,which can be either manually motorized .
* Two roller calenders help in obtatinging rubber sheets or thickness mesure more than 5mm or even more.
* 3-roll and 4-roller calender machine are commonly used in tire conveyor belts and sheeting lines.
Rubber/Plastic Calender Specification
Item | Roll Size | Width of Products (mm) | Main Power Requirement (HP) | Outline Dimension(for reference)(mm) | ||
L | W | H | ||||
1 | 12″Øx36″L | 614~762 | 40 | 4920 | 1840 | 2110 |
2 | 14″Øx42″L | 767~914 | 75 | 5160 | 2000 | 2320 |
3 | 16″Øx48″L | 919~1067 | 100 | 6174 | 2200 | 2974 |
4 | 18″Øx54″L | 1072~1219 | 125 | 6722 | 3400 | 3235 |
5 | 20″Øx60″L | 1224~1372 | 150 | 7000 | 4200 | 3440 |
6 | 22″Øx66″L | 1376~1524 | 175~200 | 7820 | 4265 | 3605 |
7 | 24″Øx72″L | 1529~1676 | 200~250 | 9075 | 4460 | 4375 |
Simptek custom calender machines for various industries manufacturers all over the world . The calenders conprise of 2 ,3 or more steel rolls that under high pressure to smooth, compress, and in some cases partially bond a nonwoven, plastic, textile , PVC, paper, rubber or another substrate. Basically , the more quantity of rollers the calendar has, the more times of the sheets are pressed and it would make higher quality and more even thickness of sheets. The rollers may be mirror-smooth, embossed with a pattern, or porous, and are usually heated with hot oil or electric elements.
Simptek provides the perfect Textile Fabric ,Pvc ,Rubber calendering technology to suit your special needs and final product demands
Safety Feature
We offer Calenders in vertical, offset as well as inverted “L”, “S”, “I” & modified “Z” type configurations.
- Bearing Protection
- Motor & Drive Safety
- Gearbox Safety
- Safety Guards
- Bearing Protection
- Roll Safety
Want to talk to our calendering experts?
If you wish to get further information like technical specifications, need a quotation, or wish to discuss different solutions, fill in the contact form and our experts will contact you shortly.